Solvent-free synthesis of Sucrose esters
Sucrose esters industrial blends are usually prepared by transesterification of fatty acid methyl esters by sucrose, in basic conditions and in a solvent that co-solubilise the reagents. To get rid of the solvent and develop more environmental-friendly methods, several attempts to react the sucrose (solid) with the fatty acid derivative (liquid) without any solvent have been described. Due to the very poor reactivity of solid sucrose in these conditions, the main products are sucrose esters with a high degree of substitution (tetraesters and over). The yield in sucrose monoesters, the most hydrophilic emulsifiers, is usually very poor.
So, to get a high yield of sucrose monoesters, is there a way to make sucrose (solid, hydrophilic) miscible to the fatty acid ester (liquid, hydrophobic) in the absence of solvent? Is there a way to get rid of the solid-solid or solid-liquid interfaces that hinder the reactivity of sucrose and without caramelizing sucrose?
By adding a divalent metal fatty acid alkanoate (e.g. magnesium or zinc stearate) to the sucrose / fatty acid ester / base mixture, an homogeneous and melted paste is obtained at 125°C. In these conditions, the reaction proceeds as an homogeneous reaction in solvent: similar kinetics, fast reaction, sucrose monoesters as the main products. Conversely, a reaction carried out without the divalent fatty acid alkanoate is heterogeneous, much slower and yields to sucrose polyesters as main products.
The homogeneity of the reaction can be explained by a possible deep eutectic of the mixture sucrose / potassium hydroxyde / magnesium stearate. It may be also related to the mesogenic and complexation properties of divalent metal alkanoates and their use as ionic liquid crystalline solvents or molten salts.
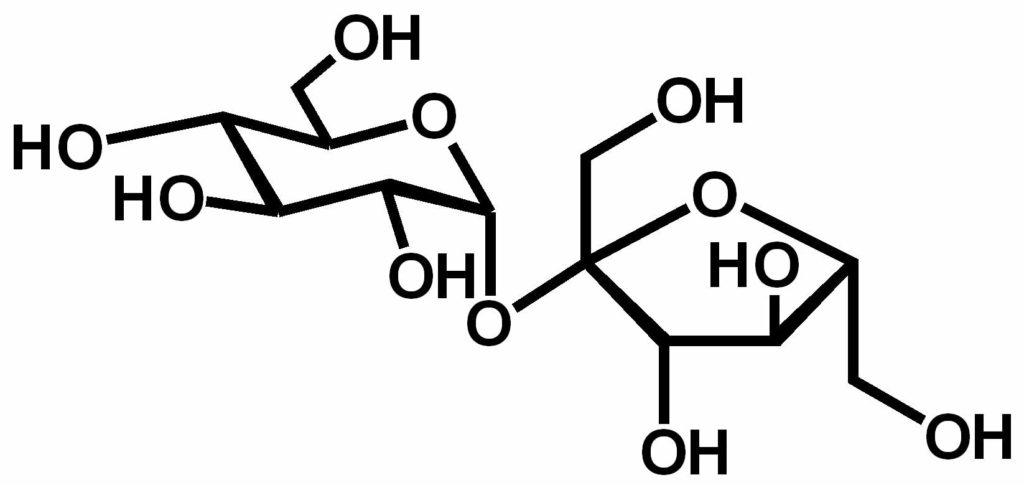
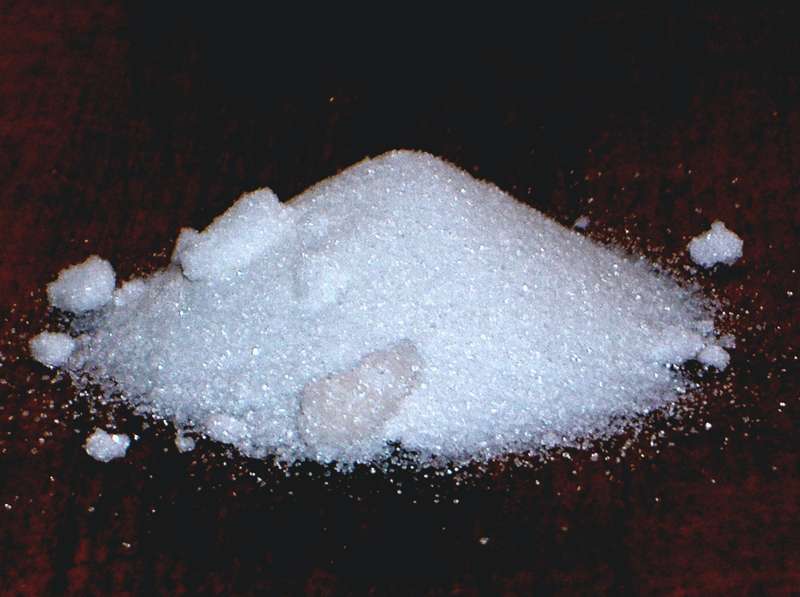
- KOH (1 eq./sucrose), magnesium stearote (0.42 eq./sucrose) 100°C, 1h, with or without H2O
- Dry under vacuum
- Methylpalmitate (0.42 eq./sucrose) 125-135°C, 4h, under vacuum
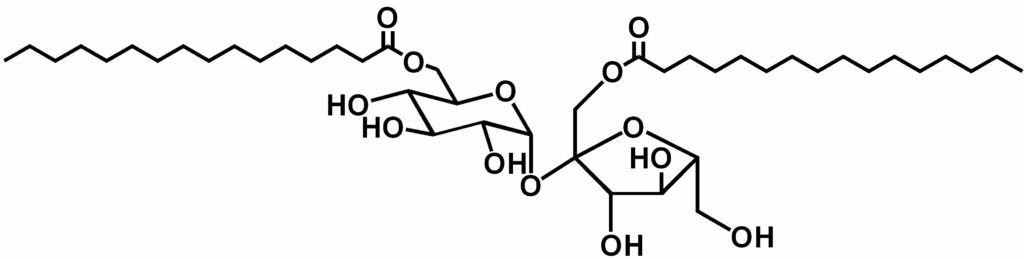
- Sucrose monoesters (41%)
- Sucrose diesters ( 33%)
Total yield = 74%
Obtained as a mixture of regioisomers
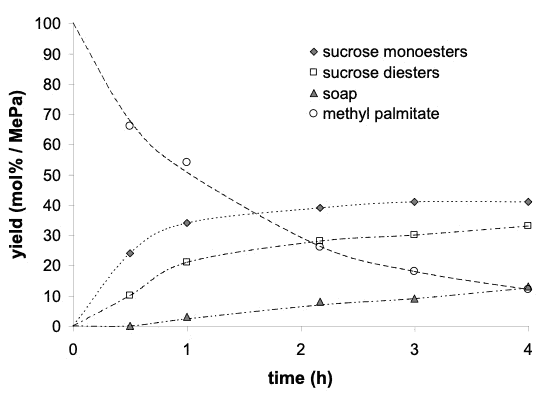
No solvent / One equivalent of magnesium stearate
The fatty acid methyl ester (methyl palmitate) is mainly converted into sucrose monoesters and diesters, as it occurs when the reaction is carried out in a solvent (such as dimethylsulfoxide).
(metal alkanoate and methyl ester have been selected with different chain length (e.g sterate and palmitate respectively, for analytical purpose)
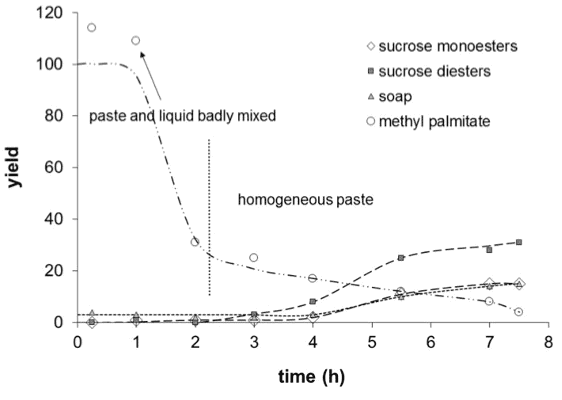
No solvent / No magnesium stearate
Without the magnesium soap, the fatty acid methyl ester (methyl palmitate) is mainly converted into soap (potassium palmitate) or sucrose fatty acid polyesters. The yield in monoesters is poor.
Recipe
Take solid sucrose, mix with one equivalent of potassium hydroxide, one equivalent of magnesium long chain alkanoate (e.g. stearate or palmitate). Heat at 100°C for one hour, then under vacuum to dry the mixture for one hour. Then add 0.42 equivalent of fatty acid methyl ester (e.g. methyl stearate or methyl palmitate). Heat at 125-135°C in a reactor for 4 hours under vacuum, striping out the methanol.
- Sucrose melting point / decomposition in caramel: 186°C
- Magnesium stearate melting point: 145°C
Drawbacks: there is a lot of fatty acid coming with the desired product, because of the 1 eq. of magnesium stearate introduced. Alcoolic extractions can separate a large part of it for recycling. The fatty acid recovered can be recycled by reaction with magnesium hydroxide or magnesium oxide. The reaction with sucrose can be performed one-pot afterward.
Publications
- Fitremann, J.; Queneau, Y.; Maître, J.-P.; Bouchu, A. Co-Melting of Solid Sucrose and Multivalent Cation Soaps for Solvent-Free Synthesis of Sucrose Esters. Tetrahedron Letters 2007, 48 (23), 4111–4114.
- Review on the green chemistry of sucrose and biorefineries perspectives for sucrose: Queneau, Y.; Jarosz, S.; Lewandowski, B.; Fitremann, J. Sucrose Chemistry and Applications of Sucrochemicals. In Advances in Carbohydrate Chemistry and Biochemistry; Horton, D., Ed.; Academic Press, 2007; Vol. 61, pp 217–292.